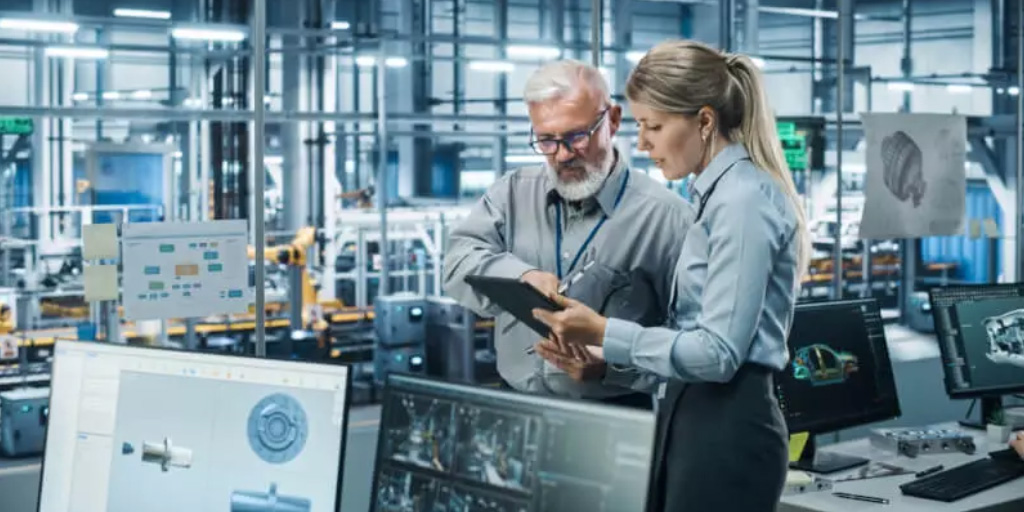
OPTIMIZATION OF TECHNOLOGICAL PROCESSES – IMPROVING ENERGY EFFICIENCY AND COST REDUCTION
As part of our services, we conduct a detailed analysis of production processes to identify specific opportunities for improving energy efficiency. By modifying technological procedures and implementing modern solutions, companies can achieve significant energy savings, reduce operational costs, and increase their competitiveness.
1. Energy Consumption Analysis of Production Processes
We begin with a comprehensive analysis of energy consumption across various technological processes. We assess energy use at each production stage, identifying the most energy-intensive and costly processes, such as:
- Energy use in heating, cooling, mechanical, and transport processes,
- Efficiency metrics for individual equipment and production lines,
- Historical and trend data analysis to identify energy consumption patterns and areas for optimization.
2. Identifying and Eliminating Energy Losses in Processes
One of the most critical optimization steps is identifying energy losses in production processes and proposing actions to reduce unnecessary energy use, such as:
- Reducing heat loss by improving thermal insulation of equipment and installations,
- Optimizing material and resource flows to reduce transport energy,
- Eliminating idle energy consumption, e.g., by automatically switching off machines during inactivity.
3. Optimization of Production Equipment Operating Parameters
Energy efficiency can often be improved by optimizing equipment and production line parameters based on data analysis and testing, adjusting factors such as:
- Temperature, pressure, and operational speed of equipment to actual process requirements,
- Equipment operation cycles and production times to reduce energy use and eliminate idle time,
- Automatic adjustment of parameters based on current production needs, minimizing excessive energy use.
4. Automation and Digitization of Production Processes
Implementing automation and modern monitoring and control systems (e.g., SCADA, IoT) allows for precise, real-time energy management, enabling:
- Automated management of machine operation cycles, enhancing efficiency and reducing energy losses,
- Quick identification of deviations in energy consumption and faults for immediate response,
- Integration with ERP (Enterprise Resource Planning) systems, facilitating production planning and control.
5. Energy Recycling and Heat Recovery from Technological Processes
Many technological processes generate excess heat that can be recovered and reused in other areas of the facility. Example solutions include:
- Implementing recuperation systems to recover heat from exhaust air or used media (e.g., water),
- Using waste heat to power other production processes, heat spaces, or preheat utility water,
- Employing heat exchangers and energy storage units to store surplus thermal energy for later use.
6. Transition to More Energy-Efficient Production Technologies
In some cases, modernization or complete overhaul of production technology can bring significant energy savings. We analyze available technologies and advise clients on their potential benefits, such as:
- Replacing energy-intensive machines with more efficient models,
- Shifting to production processes that utilize alternative energy sources, such as renewable energy-based technologies,
- Using low-temperature or low-pressure technologies characterized by lower energy consumption.
7. Virtualization and Simulation of Production Processes
Process virtualization allows for simulation of various production scenarios and their impact on energy consumption, enabling us to:
- Test different machine configurations and work schedules to find the most efficient solutions,
- Forecast energy consumption for planned technological changes, minimizing investment risks,
- Optimize production sequence and resource allocation based on real data and analyses.
8. Reducing Downtime and Minimizing Idle Operation
Extended downtimes and excessive idle equipment operation lead to energy losses. As part of process optimization, we:
- Implement maintenance schedules that minimize downtime and increase machine availability,
- Automate equipment operation cycles to shut down or enter energy-saving modes during downtime,
- Propose organizational changes for better production planning and efficient machine use.
9. Employee Training and Engagement in Energy Efficiency Management
Employee training and awareness-raising about energy efficiency are essential to optimization. We offer educational programs that:
- Inform employees about best practices for energy savings and efficient machine management,
- Encourage active participation in energy-saving initiatives, such as suggesting cost-saving ideas,
- Enhance employee involvement in energy efficiency efforts, leading to better results and a more sustainable work culture.
10. Reporting Results and Long-Term Monitoring of Progress
Following the implementation of recommendations and process optimizations, we prepare regular reports presenting achieved savings and the impact of changes. Based on monitoring results:
- We analyze efficiency metrics showing actual energy savings and cost reductions,
- Review progress towards energy goals and recommend further optimization actions,
- Continuous monitoring enables the optimization strategy to adapt to changing production and technological conditions.
Benefits of Technological Process Optimization
Optimizing technological processes brings measurable benefits, such as:
- Reduction of energy and material costs through more efficient resource use,
- Increased production efficiency and reliability, minimizing downtime and improving machine availability,
- Reduction of CO₂ emissions and environmental impact by lowering energy use and minimizing waste,
- Enhanced competitiveness through lower operational costs and implementation of modern technologies.
By optimizing technological processes, companies not only achieve cost savings but also improve their operational efficiency and strengthen their reputation as a business committed to sustainable development.