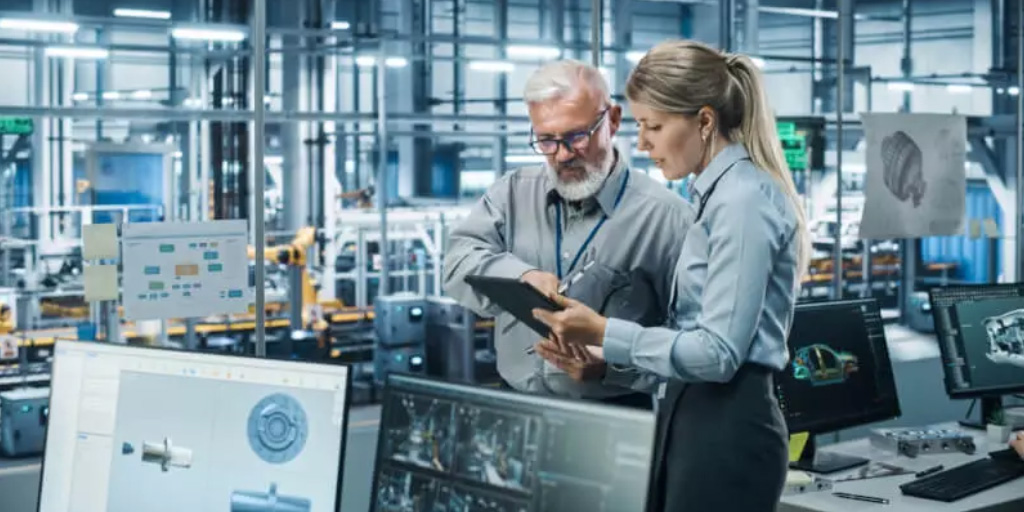
OPTYMALIZACJA PROCESÓW TECHNOLOGICZNYCH – POPRAWA EFEKTYWNOŚCI ENERGETYCZNEJ I REDUKCJA KOSZTÓW
Optymalizacja procesów technologicznych jest kluczowym elementem strategii zarządzania energią w przedsiębiorstwach produkcyjnych. W ramach naszych usług przeprowadzamy szczegółową analizę procesów produkcyjnych, wskazując konkretne możliwości poprawy efektywności energetycznej. Dzięki zmianom w procedurach technologicznych oraz wdrożeniu nowoczesnych rozwiązań przedsiębiorstwa mogą osiągnąć znaczące oszczędności energii, zmniejszyć koszty operacyjne i zwiększyć swoją konkurencyjność.
1. Analiza energochłonności procesów produkcyjnych
Na początek przeprowadzamy kompleksową analizę energochłonności poszczególnych procesów technologicznych. Oceniamy zużycie energii na każdym etapie produkcji, identyfikując procesy najbardziej energochłonne oraz te, które generują największe koszty. Przykładowo:
- Badamy zużycie energii w procesach grzewczych, chłodniczych, mechanicznych i transportowych,
- Określamy wskaźniki efektywności dla poszczególnych urządzeń i linii produkcyjnych,
- Analizujemy dane historyczne i trendowe, aby zidentyfikować wzorce zużycia energii oraz określić potencjalne obszary do optymalizacji.
2. Identyfikacja i eliminacja strat energii w procesach
Jednym z najważniejszych elementów optymalizacji jest identyfikacja strat energii w procesach produkcyjnych. Na tej podstawie proponujemy działania, które pozwalają ograniczyć niepotrzebne zużycie energii, np.:
- Zmniejszenie strat ciepła poprzez poprawę izolacji termicznej urządzeń i instalacji,
- Optymalizację przepływu materiałów i surowców, co pozwala zredukować energię potrzebną do ich transportu,
- Wyeliminowanie strat energii wynikających z pracy urządzeń w trybie jałowym, np. poprzez automatyczne wyłączanie maszyn w okresach bezczynności.
3. Optymalizacja parametrów pracy urządzeń produkcyjnych
Często możliwa jest poprawa efektywności energetycznej poprzez optymalizację parametrów pracy urządzeń i linii produkcyjnych. Na podstawie analizy danych i testów, dostosowujemy parametry takie jak:
- Temperatura, ciśnienie i prędkość pracy urządzeń do rzeczywistych wymagań procesowych,
- Cykle pracy urządzeń i czas produkcji w celu redukcji zużycia energii i eliminacji pracy w trybie jałowym,
- Automatyczne dostosowywanie parametrów w zależności od aktualnych potrzeb produkcyjnych, co minimalizuje nadmiarowe zużycie energii.
4. Automatyzacja i digitalizacja procesów produkcyjnych
Wdrożenie automatyzacji oraz nowoczesnych systemów monitorowania i sterowania (np. SCADA, IoT) pozwala na precyzyjne zarządzanie zużyciem energii w czasie rzeczywistym. Automatyzacja umożliwia:
- Zautomatyzowane zarządzanie cyklami pracy maszyn, co zwiększa wydajność i zmniejsza straty energetyczne,
- Szybką identyfikację odchyleń od norm zużycia energii oraz awarii, co pozwala na błyskawiczną reakcję,
- Integrację z systemami ERP (Enterprise Resource Planning), co ułatwia planowanie produkcji i kontrolę nad procesami technologicznymi.
5. Recykling energii i odzysk ciepła z procesów technologicznych
W wielu procesach technologicznych generowane jest nadmiarowe ciepło, które można odzyskać i ponownie wykorzystać w innych częściach zakładu. Przykładowe rozwiązania obejmują:
- Wdrożenie systemów rekuperacji, które pozwalają na odzyskiwanie ciepła z wywiewanego powietrza lub zużytych mediów (np. wody),
- Wykorzystanie ciepła odpadowego do zasilania innych procesów produkcyjnych, ogrzewania pomieszczeń czy podgrzewania wody użytkowej,
- Zastosowanie wymienników ciepła i akumulatorów energii, które magazynują nadmiarową energię cieplną i udostępniają ją w momencie zapotrzebowania.
6. Zmiana technologii produkcji na bardziej energooszczędne
W niektórych przypadkach modernizacja lub całkowita zmiana technologii produkcji może przynieść znaczące oszczędności energetyczne. Analizujemy dostępne technologie i doradzamy klientom w zakresie ich potencjalnych korzyści, takich jak:
- Zastąpienie energochłonnych maszyn bardziej efektywnymi modelami,
- Przejście na procesy produkcyjne wykorzystujące alternatywne nośniki energii, np. technologie oparte na odnawialnych źródłach energii,
- Zastosowanie technologii niskotemperaturowych lub niskociśnieniowych, które charakteryzują się niższym zużyciem energii.
7. Wirtualizacja i symulacje procesów produkcyjnych
Wirtualizacja procesów pozwala na symulację różnych scenariuszy produkcyjnych oraz ich wpływu na zużycie energii. Dzięki modelowaniu procesów produkcyjnych możemy:
- Testować różne konfiguracje maszyn i harmonogramy pracy, aby znaleźć najbardziej efektywne rozwiązania,
- Przewidywać zużycie energii dla planowanych zmian technologicznych, co minimalizuje ryzyko inwestycyjne,
- Optymalizować sekwencję produkcyjną oraz alokację zasobów w oparciu o realne dane i analizy.
8. Skracanie czasu przestojów i minimalizowanie pracy jałowej
Długi czas przestojów oraz nadmierna praca urządzeń w trybie jałowym prowadzą do strat energii. W ramach optymalizacji procesów:
- Wprowadzamy harmonogramy konserwacji, które minimalizują przestoje i zwiększają dostępność maszyn,
- Automatyzujemy cykle pracy urządzeń, aby wyłączały się lub przechodziły w tryb oszczędny w okresach przestojów,
- Proponujemy organizacyjne zmiany, które pozwalają na lepsze planowanie produkcji i uniknięcie nieefektywnego wykorzystania maszyn.
9. Szkolenie i zaangażowanie pracowników w zarządzanie efektywnością energetyczną
Szkolenia oraz zwiększenie świadomości pracowników dotyczące efektywności energetycznej są nieodzownym elementem optymalizacji. Oferujemy programy edukacyjne, które:
- Informują pracowników o najlepszych praktykach związanych z oszczędzaniem energii i efektywnym zarządzaniem maszynami,
- Zachęcają do aktywnego uczestnictwa w inicjatywach energetycznych, takich jak zgłaszanie pomysłów na oszczędności,
- Podnoszą zaangażowanie pracowników w działania na rzecz efektywności energetycznej, co prowadzi do lepszych wyników i bardziej zrównoważonej kultury pracy.
10. Raportowanie wyników i długoterminowe monitorowanie postępów
Po wdrożeniu rekomendacji i optymalizacji procesów produkcyjnych przygotowujemy regularne raporty, które przedstawiają uzyskane oszczędności oraz efekty przeprowadzonych zmian. Na podstawie wyników monitorowania:
- Dokonujemy analizy wskaźników efektywności, które pokazują realne oszczędności energii i redukcję kosztów,
- Przeglądamy postępy w realizacji celów energetycznych i proponujemy dalsze działania optymalizacyjne,
- Regularne monitorowanie pozwala na dostosowanie strategii optymalizacji do zmieniających się warunków produkcyjnych i technologicznych.
Korzyści z Optymalizacji Procesów Technologicznych
Optymalizacja procesów technologicznych przynosi firmie wymierne korzyści, takie jak:
- Redukcja kosztów energii i materiałów poprzez bardziej efektywne wykorzystanie zasobów,
- Zwiększenie wydajności i niezawodności produkcji, co minimalizuje przestoje i poprawia dostępność urządzeń,
- Ograniczenie emisji CO₂ i wpływu na środowisko dzięki zmniejszeniu zużycia energii i minimalizacji strat,
- Wzrost konkurencyjności poprzez obniżenie kosztów operacyjnych i wdrożenie nowoczesnych technologii.
Dzięki optymalizacji procesów technologicznych przedsiębiorstwo zyskuje nie tylko oszczędności, ale również poprawia swoją efektywność operacyjną, wzmacniając jednocześnie swój wizerunek jako firma dbająca o zrównoważony rozwój.